作為生產(chǎn)制造過程中必不可少的一步,表面缺陷檢測廣泛應(yīng)用于各工業(yè)領(lǐng)域,包括3C、半導(dǎo)體及電子、汽車、化工、醫(yī)藥、輕工、軍工等行業(yè),催生了眾多上下游企業(yè)。自20世紀開始,表面缺陷檢測大致經(jīng)歷了三個階段,分別是人工目視法檢測、單一機電或光學(xué)技術(shù)檢測以及機器視覺檢測。
人工目視法起源最早,應(yīng)用最廣,雖然人工智能及機器視覺等先進檢測技術(shù)逐漸成熟,但依靠肉眼進行缺陷檢測仍然占據(jù)較大的比重,并廣泛存在于中小企業(yè)中。據(jù)統(tǒng)計,當(dāng)前80%以上的工業(yè)表面缺陷檢測仍依賴于人工檢測法,每天產(chǎn)品線上進行人工檢測的工人數(shù)量超350萬人。以富士康,伯恩光學(xué)等為代表的制造企業(yè)招聘大量的質(zhì)檢工人,采取流水線的形式進行檢測。然而,隨著人口紅利的消失,以及工作枯燥、自由度低、薪酬較少,愿意從事質(zhì)檢的越來越少,用工難問題愈發(fā)凸顯。
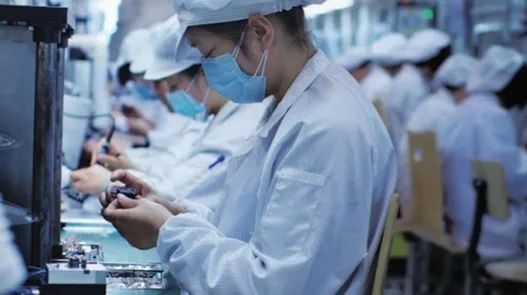
從當(dāng)前的發(fā)展趨勢來看,機器視覺等先進檢測系統(tǒng)將逐漸取代人工,這主要是因為人工檢測法具有以下缺點:
1、勞動強度大、檢測穩(wěn)定性及一致性差
人工檢測法需要工人處于固定工位上,用肉眼觀察產(chǎn)品來判斷有無缺陷。長時間的檢測工作容易對人眼造成傷害,特別是在檢測玻璃、金屬等強烈反光的物體表面時。冶金、軌道交通、機械制造等行業(yè)內(nèi)的缺陷檢測場景噪聲大、煙塵重、危險性高,長期處于惡劣的工作環(huán)境對工人的身心健康造成惡劣影響。受工人的情緒浮動、技術(shù)水平、判斷標準、個體差異等因素影響,甚至無法保障同一批次產(chǎn)品的檢測穩(wěn)定性和一致性,使得產(chǎn)品質(zhì)量上下浮動,參差不齊。
2、自動化程度低、生產(chǎn)效率低
由于工人的質(zhì)檢效率上限較低,同時人工成本又越來越高,企業(yè)為保障生產(chǎn)效率,一般采取抽樣檢測的策略。一批產(chǎn)品中隨機抽取少量產(chǎn)品來評估整批產(chǎn)品的質(zhì)量,其嚴格程度遠遠低于全面檢測。因此人工進行缺陷檢測時容易陷入一種矛盾: 質(zhì)量控制和生產(chǎn)效率二者不可兼得。這種矛盾在面料、帶鋼、薄膜等產(chǎn)品的表面缺陷檢測中尤為突出。這一類產(chǎn)品多為高速連續(xù)性生產(chǎn),當(dāng)生產(chǎn)速度高于3m/s時,人眼便難以分辨出其中的缺陷。
3、難以形成精益化生產(chǎn)
質(zhì)量是制造出來的,而不是檢測出來的。檢測只是一種事后補救,不但成本高而且無法保證不出差錯。許多檢測不僅需要判斷產(chǎn)品的外觀質(zhì)量,還要記錄并統(tǒng)計缺陷的位置、尺寸和數(shù)量等數(shù)據(jù)。傳統(tǒng)的人工檢測使用紙筆記錄質(zhì)檢結(jié)果,檢測數(shù)據(jù)不全且分散,無法形成具有價值的反饋信息來指導(dǎo)精益化生產(chǎn)。
4、招工難、用工難、培訓(xùn)難、成本高
工作待遇低、工作時間長、勞動強度大等因此直接影響了招工的穩(wěn)定性。越來越多年輕人寧愿去送外賣也不愿進入工廠工作,使得缺陷檢測這種傳統(tǒng)的勞動密集型崗位很難招聘到工人,培訓(xùn)后的熟練工又存在人才流失嚴重等問題。人口紅利消失的趨勢不可逆轉(zhuǎn),用人成本不斷攀升,上線自動化缺陷檢測系統(tǒng)已從“可選”轉(zhuǎn)向“必選”。
為了在不斷變化和競爭愈發(fā)激烈的市場中占據(jù)優(yōu)勢,企業(yè)既要不斷提高產(chǎn)品質(zhì)量標準以滿足客戶需求,又要不斷提升生產(chǎn)線的效率以適應(yīng)市場的快節(jié)奏。采用自動化、智能化的表面缺陷檢測方法是兼顧質(zhì)量與效率的重要手段。